New research could change the way plastic is recycled, offering attractions a greener alternative in the future

Tom Anstey | Planet Attractions | 03 Feb 2021
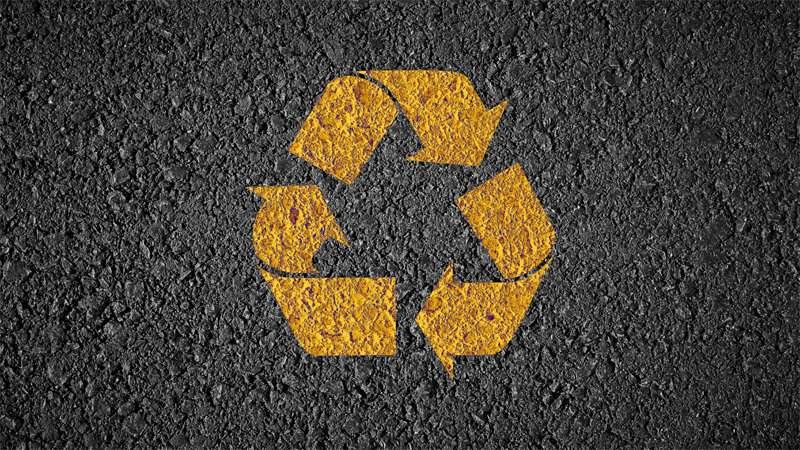
Multilayer plastic is primarily used in attractions for food packaging Credit: Canva
Engineers at the University of Wisconsin-Madison (UOW) have pioneered a new method of recycling, which could cut down on millions of tons of plastic waste worldwide.
An estimated 100 million tons of multilayer thermoplastics are produced globally every year, with around 40% of that waste coming from the manufacturing process itself.
In visitor attractions, these plastics primarily come in the form of food packaging, with this kind of plastic able to keep food fresher for longer. With many attractions making moves to eliminate single-use plastics, the new innovation from UOW could be a game changer.
Called Solvent-Targeted Recovery and Precipitation (STRAP) processing, the pioneering recyling method sees the polymers in plastic reclaimed using solvents.
Through the process, professors of chemical and biological engineering, George Huber and Reid Van Lehn, and their students used STRAP to separate the polymers in a commercial plastic composed of common layering materials polyethylene, ethylene vinyl alcohol, and polyethylene terephthalate.
As a result, the separated polymers became chemically similar to those used to make the original plastic film, meaning that the recovered polymers can be used to create new plastic material, closing the ‘recycling loop’.
“We’ve demonstrated this with one multilayer plastic,” said Huber. “We need to try other multilayer plastics and we need to scale this technology.”
The goal of the research is to eventually develop a system that will allow researchers to find solvent combinations to recycle a range of multilayer plastics.
The team also hopes to look at the environmental impact of the solvents it uses and establish a database of green solvents for the process.
Technology
|
|
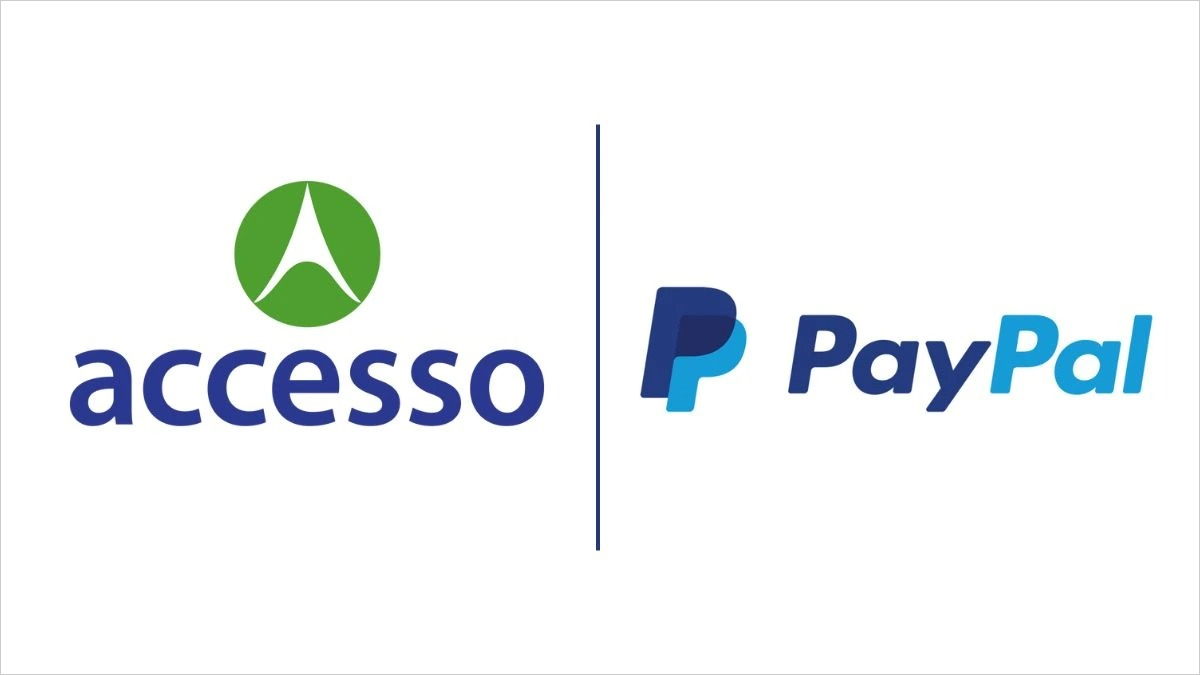
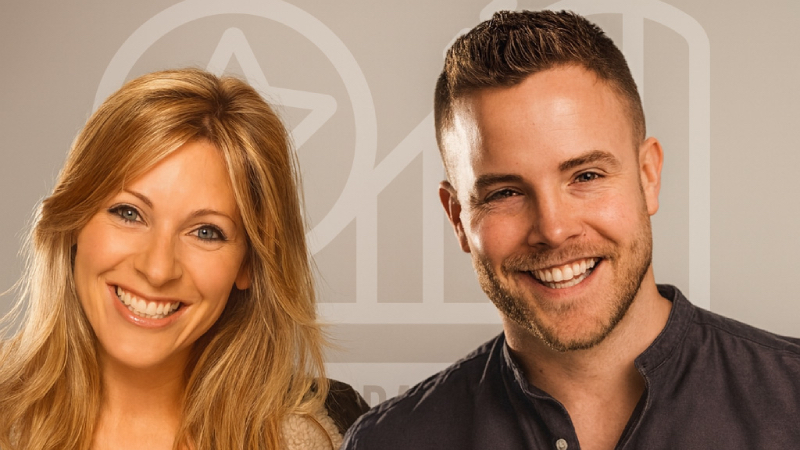
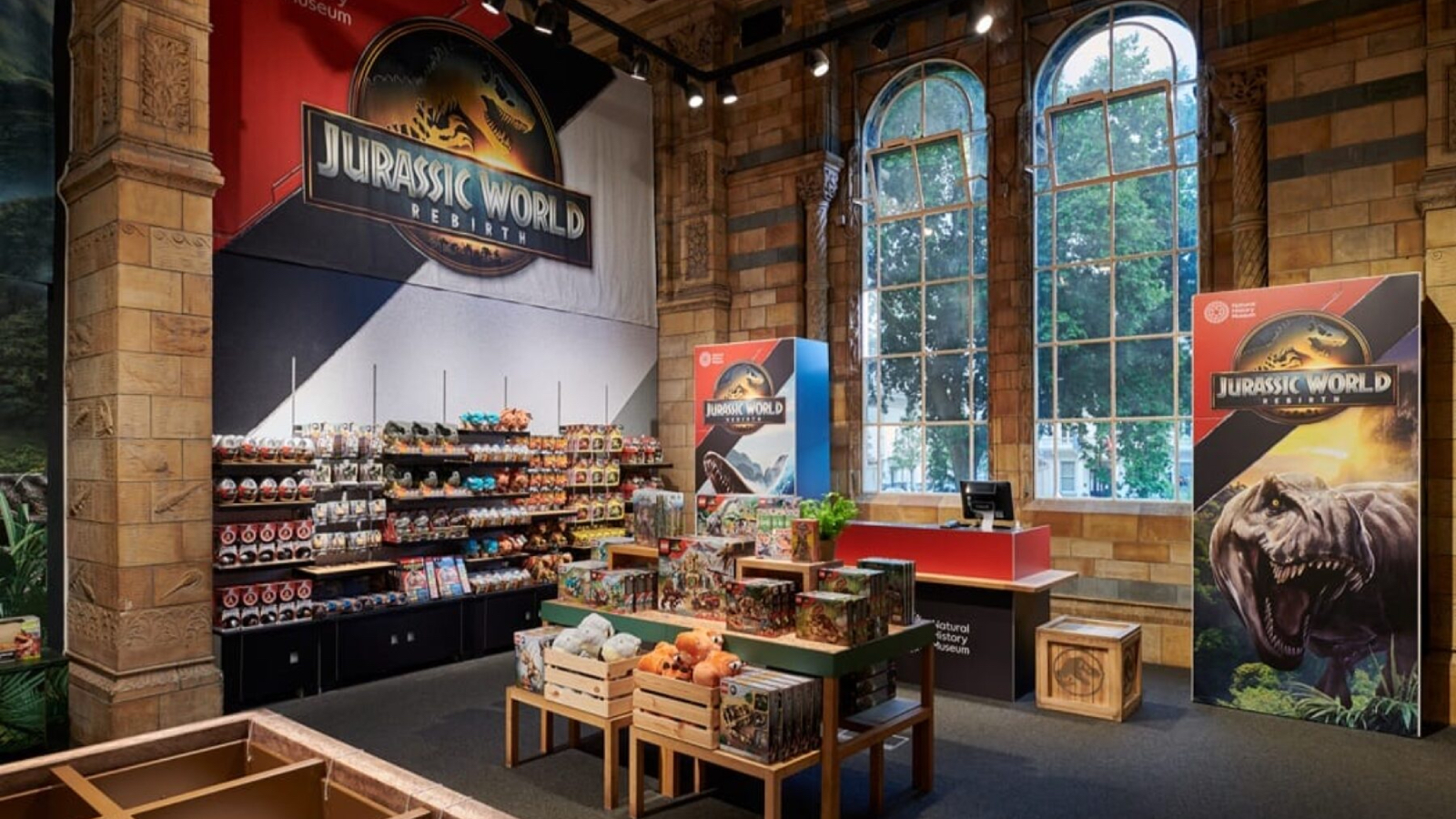
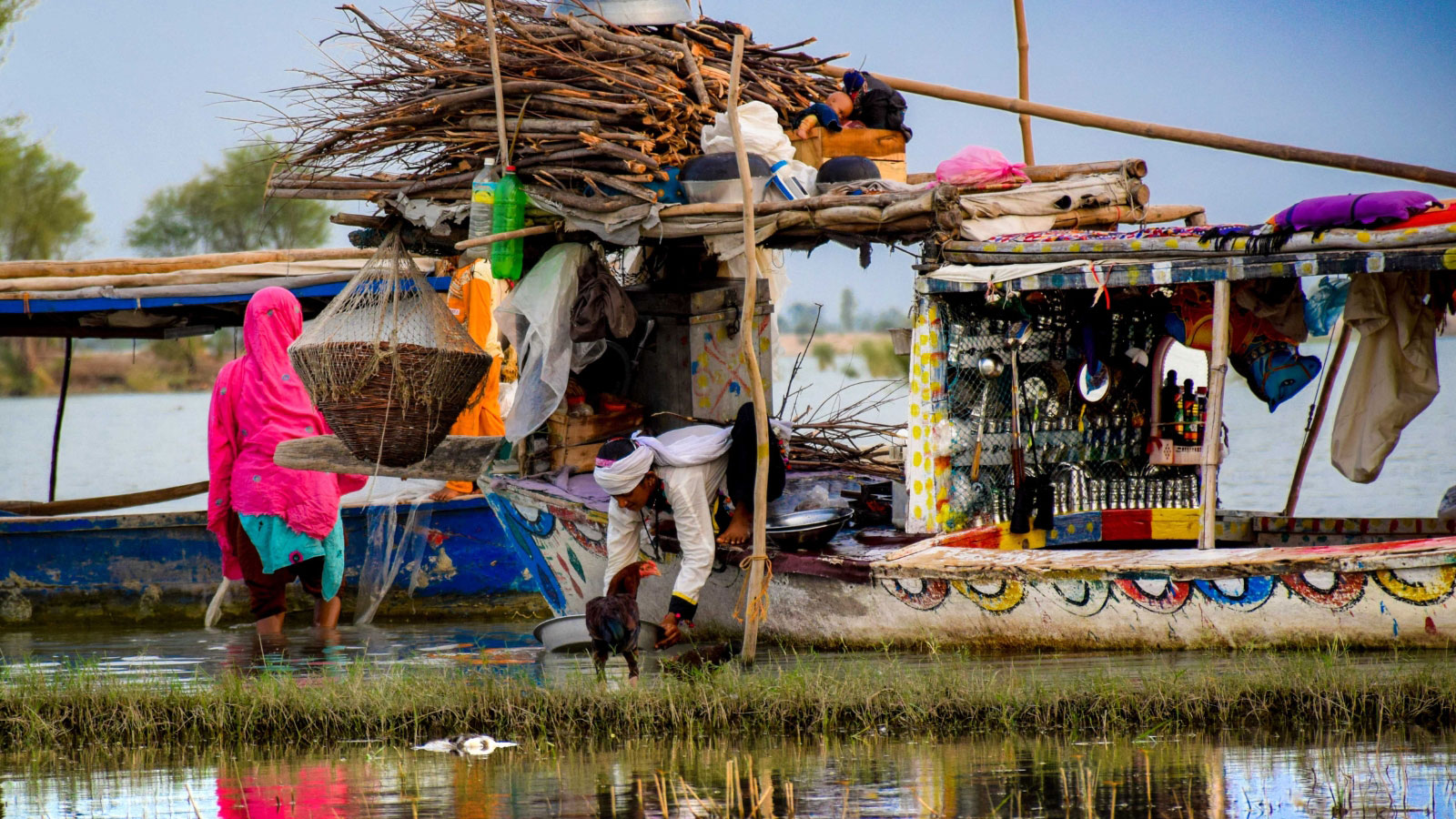
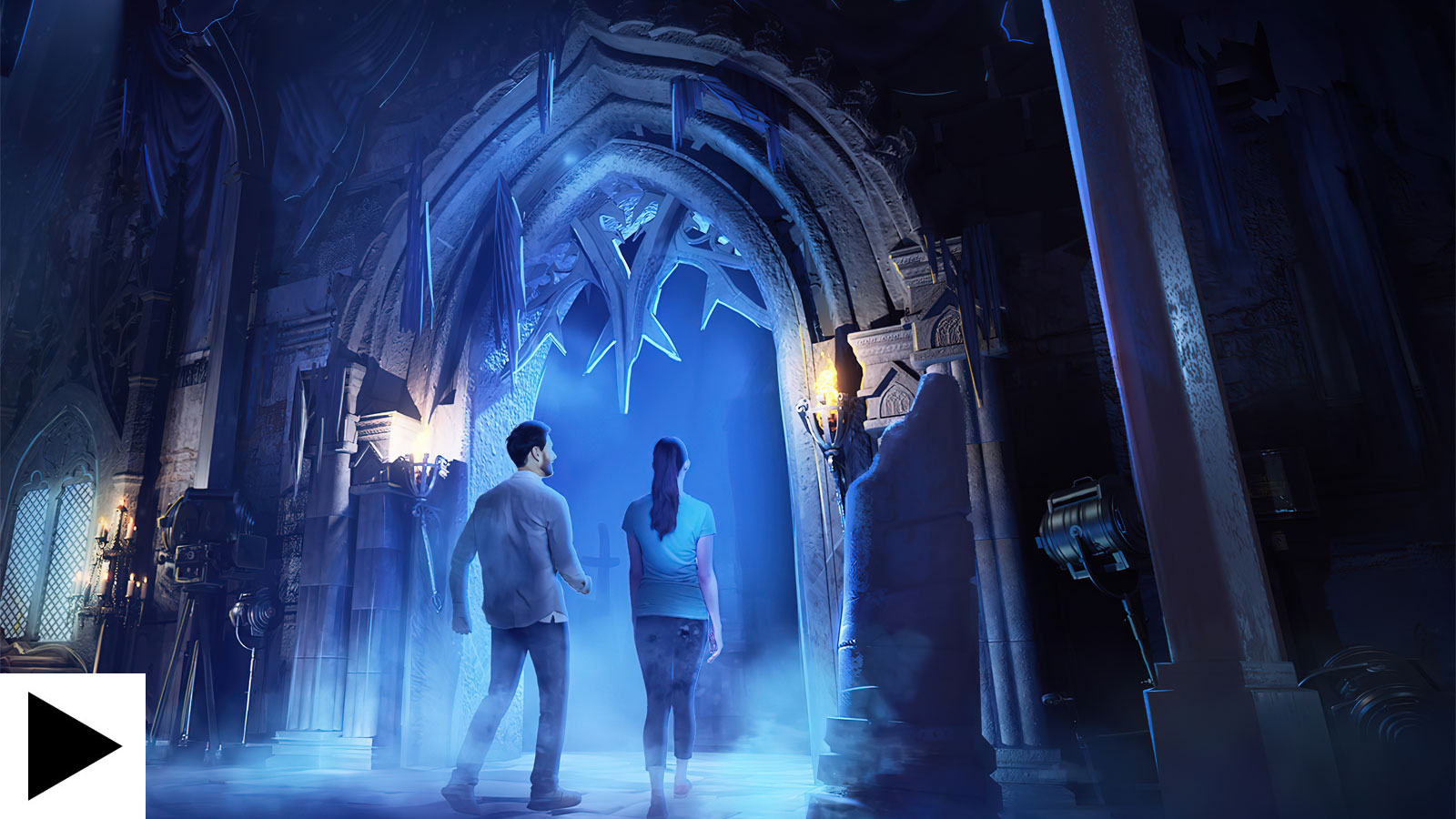
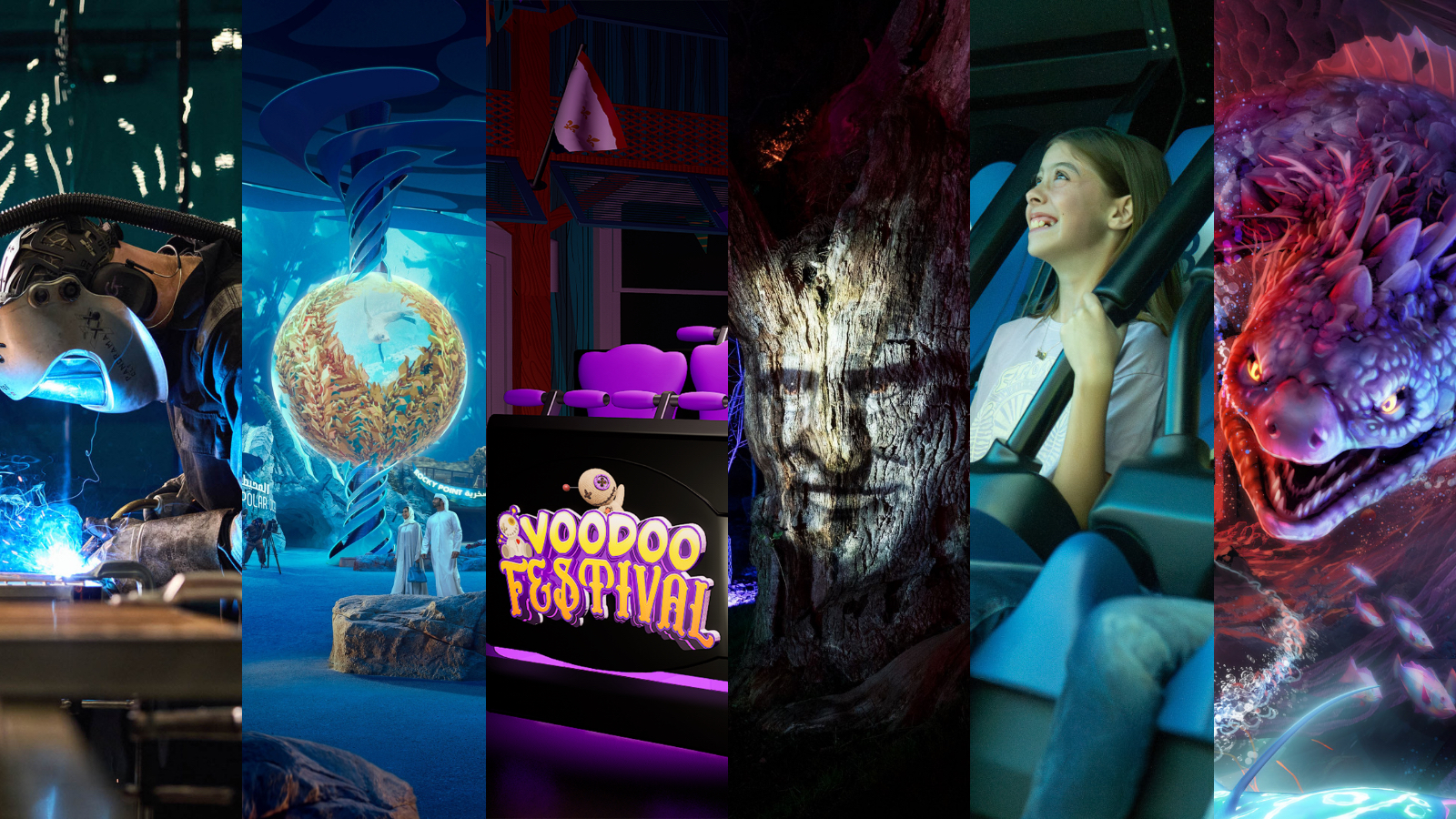
Supplier Showcase 2025: The biggest attractions projects landing worldwide this year
|